【第2回】Pharma4.0と製造現場のデジタル化施策 製造ITの歴史と「Quality by Design」
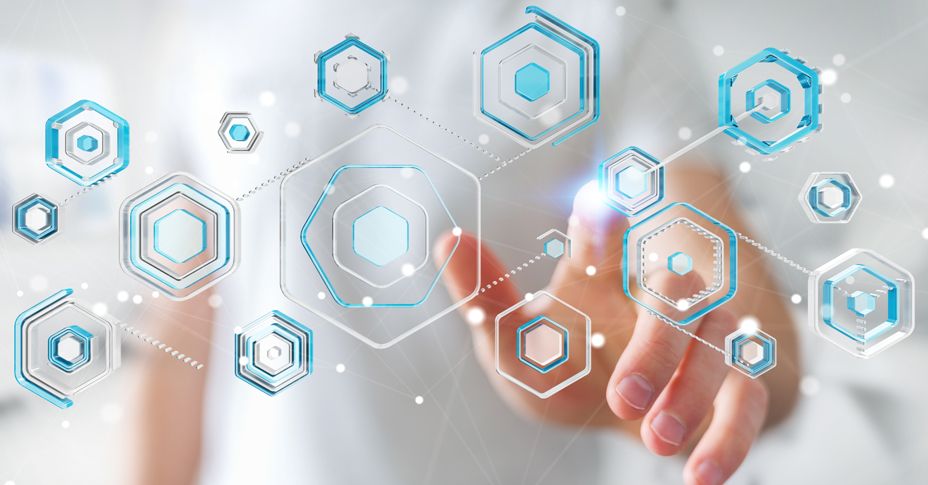
引き続き、医薬製造業の課題を取り上げ、解決に向けた当社の各種取り組みをご紹介する。
Pharma4.0 スマートファクトリーへの挑戦 Challenge to the Pharma4.0
本コラムでは、Pharma4.0スマートファクトリーに向けた医薬製造業の課題を取り上げ、その解決に向けた当社の各種取り組みをご紹介します。大きな基盤づくりの方法論から、各種課題解決ツールまで、幅広くご紹介しますのでご期待ください。
1.製造ITの時代背景を振り返る 1990年代~現在
製造ITの時代背景を振り返り、何故、現在のシステム基盤になったかを考察するうえでの参考となればと思います。
1990年代から、製造業では統合型業務パッケージERP(Enterprise Resource Planning)で基幹業務システムのリプレイスを進め、原価管理の一元化が進みました。
これを下支えしたのが、製造現場の制御系システム(SCADA、HMI、DCSなど)と、指図情報を提供し工程実績情報を収集蓄積するMES(Manufacturing Execution System)です。
2000年代からは、製造現場の更なる効率化追求のために、ネットワークカメラを活用しての製造作業コントロールを採用する企業が増えてきました。更に、IE技法(Industry Engineering=作業研究・生産工学)を用い、作業のムリ・ムダ・ムラを無くし、仕事の価値を高める考え方として製造現場にKPI(Key Performance Indicator)を導入し、KPIに応じた目標設定と実績収集、分析、改善にチャレンジする企業が出てきました。
2011年、米国シスコシステムズは、「RFIDをつけたモノ」のみならず、製品そのものにITが組み込まれ、インターネットに接続されるように発展した時代が到来したことを指摘し、IoTが広がり始めました。また、ドイツでは、2011年から産官学共同で、製造拠点としてのドイツのポジションの維持、拡大に向け、Industrial 4.0(第4次産業革命)と呼ばれる取り組みを開始し、日本では2015年に政府が「『日本再興戦略』改訂2015」にて、鍵となる施策のひとつとして、「IoT・ビッグデータ・人工知能等による産業構造・就業構造の変革の検討」を掲げ、国家戦略としての活動がスタートしております。現在は、Society5.0として、サイバー空間(仮想空間)とフィジカル空間(現実空間)を高度に融合させたシステムにより、経済発展と社会的課題の解決を両立する、人間中心の社会(Society)の実現に向けた施策が展開されています。
医薬品業界では、Industrial 4.0を医薬品仕様にしたPharma4.0の取り組みにより、取得したデータをもとに、自律的に調整を行うシステムへの転換を進めています。このコンセプトは、10年以上前からスタートしているQuality By DesignおよびProcess Analytical Technology (PAT)の原則に基づくものですが、その適用範囲は、自動化プロセスに留まるものではないと考えています。
2.何故、医薬品製造領域のDXが難しい、保守的と言われるのか
医薬品製造の領域は、他業種と比較して“難しい”と言われております。その理由はなぜでしょうか。その背景に、バリデーション活動があると考えられます。
ヘルスケア(医薬品、医療機器製造)業界ではバリデーションと呼ばれる活動が要求されます。
これは上記の品質保証活動(各種仕様書作成から試験検査、納入)に加えて、ヘルスケア企業が公的機関(厚生労働省、米国FDA、EU PIC/Sなど)からの法規制要求である製造規範GMPを遵守していることを確認するための活動で、ヘルスケア企業が主体で対応するものです。ヘルスケア業界のバリデーションは品質保証活動の中の各種検証(試験、検査、レビュー、監査など、)を通して、ヘルスケア製品が確かに顧客の要求や意図にかない、運用後も高品質のヘルスケア製品を製造することができると確信するための文書化作業です。使用する設備機器やシステムも要求を満たしている必要がありバリデーションが必要です。設備機器やシステムの供給者は、品質保証活動を実施し、文書化し提出、あるいは提示することで顧客のバリデーション活動を支援します。
そして、運用開始後は、変更管理を行うことになりますが、もし、製造法の改良に際し、当局への申請情報の変更に影響する場合は、当局へ変更申請を行われなければならず、その申請から承認までにはかなりのリソースが必要になるため、たとえ製造工程を変えることによって品質が良くなるとしても、よほどのメリットがない限り申請は見送られることも往々にありました。、このことから、医薬品業界においては他業種と比べて製造の技術革新の恩恵にあずかることが少なかったと考えられます。
これらの背景の積み重ねにより、工場内にあるシステムそれぞれが固定化され、固定化されたシステムに小規模改修を加えて連携を図ることにより複雑化を招くことから、変更・改修の難易度が増すことになります。そして、自社の仕組みを理解した人材・スキルの継承が難しくなり新たな挑戦が難しくなったのではないでしょうか。
2ページ中 1ページ目
コメント
/
/
/
この記事へのコメントはありません。
コメント