再生医療等製品の品質保証についての雑感【第68回】
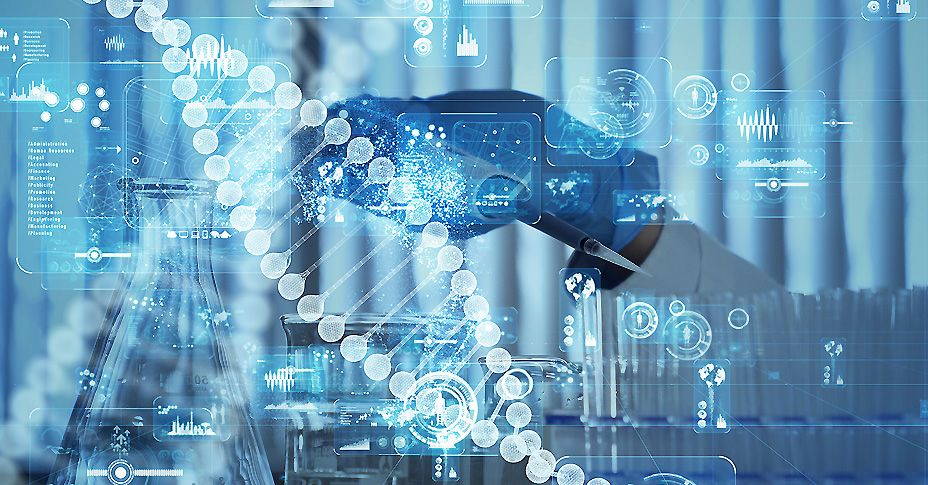
同種MSC製品等の製造工程開発において、考えられる事例の1つを述べる。
第68回:再生医療等製品の製品開発と製造工程開発とQbD (7)
~ 製造工程開発をはじめる(5) ~
はじめに
前回、下図(再掲)における、治験開始前に実施する製造工程開発の、設計-1から設計-3について概説しました。設計-3における目標は、「実製造スケールと相同」する製造工程ですが、具体的にはどのように構築すればよいのでしょうか。今回は、同種MSC製品等の製造工程開発において、考えられる事例の1つを紹介します。
図. 再生医療等製品のQbDアプローチと製造工程開発の手順に関する考え方 【再掲】
● 相同性ある製造工程(設計-3)に至る考え方の一例
細胞加工製品のライフサイクルを考慮した製品開発を行う上で、開発部門から製造部門への技術移管において課題となるのは、下図(図1)に示すように、製品設計時において実施される、機能設計に含まれる原料細胞特性と環境特性(細胞源、培地等)の理解不足(課題1)、あるいは、治験前の製造工程設計時において生じる、治験製品製造と実製造のギャップを考慮した作業特性の理解不足(課題2)が挙げられると認識します。これらの課題は、開発する製品の特性により、求められる工程の理解(工程解析技術)の考え方が異なり、ユニークな対応が求められます。
図1. 製品設計から製造工程開発において技術移管の課題が生じるポイント
例えば同種MSC製品においては、以前(第62回)にもお話しした通り、製品の有効性に直結して、選択可能な重要な物質特性(CMA)は原料細胞です。同時に、使用する培地等が、目的細胞の品質特性を決定する主工程(バイオプロセス)における、重要な工程パラメータ(CPP)に相当します。
製品の機能設計では、十分な工程解析技術が構築されていなければ、培地等をリーズナブルに変更することは非常に難しいです。そのため、現状では、製品開発において、製品のライフサイクルの変更管理に対応した培地等の開発を行うことは難しいと考えます。
2ページ中 1ページ目
コメント
/
/
/
この記事へのコメントはありません。
コメント