【第7回】私が経験した(GMP)医薬品製造にまつわる話
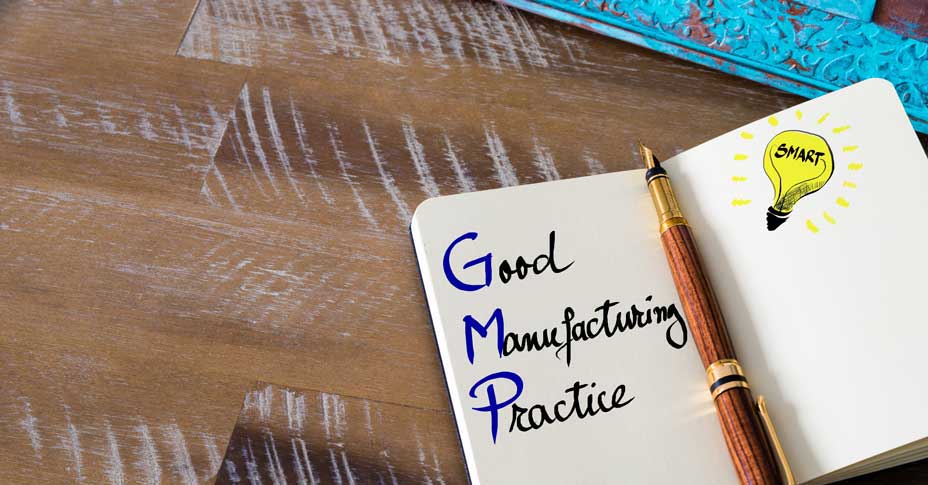
逸脱について。
なぜなぜ分析は、言い訳を省く。
逸脱など発生した場合、なぜなぜ分析で真因まで突き詰めるために回数を5回ほど実施している例をよくお聞きします。
人のせいなどの言い訳を起用せずに数回繰り返すうちに仕組み・システムの内容になるまで行うと本にありました。
すべては、品質システムの欠落が原因のはずです。だれかのせいだでは、幼稚です。
現場に出向き、最初はうまくいかなくてもいいです。改善意識をもって現場が自律神経的行動になって、自分たちでデトックスする方がみんな参加しやすくなり職場能力が向上します。
品質システムは、現場の土壌あって醸成する。
どんなに立派な品質システム文書があっても、まずは製造のパラダイムを刺激し、デトックスをして自律神経的な大人の組織にしていくべきです。そうすれば開発や物流、他のホワイトカラーも共鳴していきます。いくら高価なコンピューターシステムもこれがなくては力を出せません。もしよければTPS(トヨタ生産方式)を参考にしてください。
今こそ、「後工程は、お客様」を意識して自社の現場を巡回してください。
必ず、そこにquality cultureの醸成の鍵があります。
物流が物留になっていないか?
良い工場は、倉庫を見れば大体わかります。FDA査察も現場へ行って帰ってくる場所である倉庫の管理がダメならよい報告はでません。
製品か?原材料か?最適な管理数と管理状態(大きく見やすい表示)(合・否)がしっかりしてない場合、現場においてもそのような状態で保管されていると想像できます。
流れるように管理されてない場合、リスク(コスト・品質など)を起こしやすい滞留をおこして危険状態と予想できます。
在庫管理が明確にされていないことこそ、生産管理は信用できません。
※整理・整頓・清掃・清潔・躾 5Sを製造の第一確認項目です。
意外に見ています共有場所の5S
共有場所ですと、食堂・会議室・廃棄物置場・喫煙、休憩室や工場外周の清掃(草取りなど)があります。私は草取りやたばこ掃除を自主的に行っていた経験があります。このような行動に自主的に一人二人と増えない会社は、だめです。また、共有区域とくにトイレがきれいか?は調査員はしっかり確認すべきです。
ここが綺麗でなければ、現場や事務所もだめなことが多いです。綺麗でも調査対応の臨時です。
傘立ても、無造作に使わない錆びた傘を置きっぱなしや下駄箱の私物も見分ける技です。
基本は、社員が清掃するのが会社です。その基本ができていない会社に大切な製品を、扱ってもらいたくないはずです。
※調査員は、EHS(安全衛生)の観点もしっかり見てほしい。人にやさしくない=製品にたいしても同じでしょう。
CAPAは、会社の実力
CAPAは、その会社・製造所の実力に影響されます。ことが起きても、対応する自主的行動と観察力・洞察力を現場に任せていない場合、同じ問題と同じ流失防止(検査)のオンパレードになっているはずです。自分達の会社が、顧客から信頼されるためです。楽しく前向きな土壌をみんなで(経営者も)作れないからCAPAでやる気がわかります。
やる気は、ホワイトカラー(営業や開発、品証、生産管理など)も同じです。
2ページ中 1ページ目
コメント
/
/
/
この記事へのコメントはありません。
コメント