ゼロベースからの化粧品の品質管理【第31回】
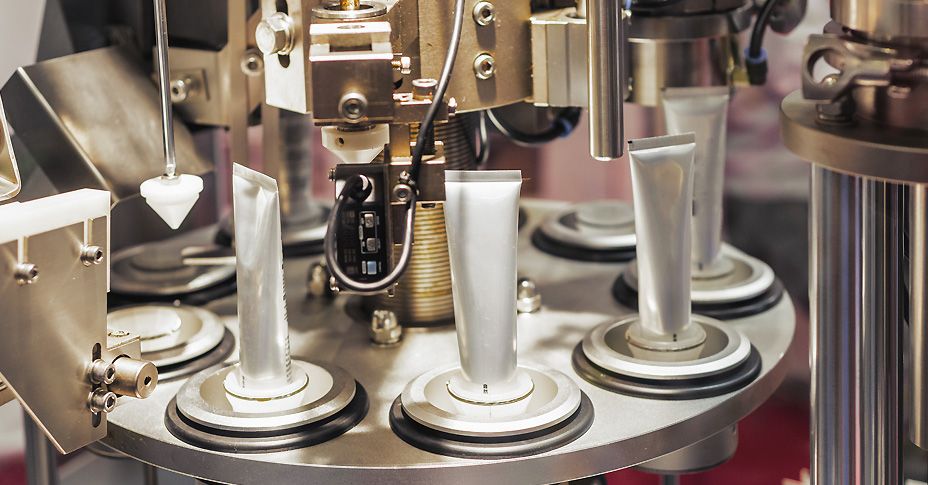
化粧品品質保証体制の構築について解説をする。
化粧品GMPで不備となり易い事項 ①是正処置~有効性評価
前回まで、化粧品のGMP管理体制の構築に向けて手順書を作成する上での留意点について30回に分けて説明させて頂きました。この話をしていく中で、手順書としては確かに存在しているものの、その会社にとって本当に活用できる状態であるのか疑問を感じるケースが多々ありました。つまり、実務の面から実践的な運用の肝が理解されていないのではないかと感じるケースや、雛形をそのまま手順書として制定し運用に結び付かない単なる表面的な対応の手順書が多いように感じています。
化粧品GMPは既に14年以上運用されている事項で、コピペの手順書でも民間認証を受けておられる製造所が多いことから、過剰の要求と言われることを重々承知の上で、敢えて査察等を通してトラブル発生件数の減少、発生防止に必須と考える事項について今回以降お話させて頂こうと思います。
今回は、逸脱に対する逸脱管理報告書が作成されている中で、是正処置の有効性評価について課題を感じていることから、再度『逸脱管理』における効果的な『是正処置』とその処置に関する『有効性評価』の進め方について考えてみたいと思います。特に、逸脱発生がうっかりミスの場合に、教育の実施で納めてしまっているケースが気になりましたので、モデルケースを示させて頂きますので、一緒に考えてみましょう。
1. GMPで要求されている逸脱管理の手順(概要)
逸脱発生⇒全ての逸脱内容を記録⇒品質への影響を評価⇒所定の処置⇒必要な場合には是正処置を取る⇒再発防止策の構築⇒再発防止策の有効性評価が全体のフローです。
勿論、逸脱が発生したとしても全ての逸脱に対して是正処置を行う必要はありません。この点は、全て是正処置を行うことで運用されている製造所がありますが、全てを対象にすることは事務処理のマンパワー負荷の増加でしかないため、重み付けの管理が必要と考えます。つまり、製品の品質に及ぼす影響を判断して、その事象が再発しているものでないことと品質への影響が殆どないと判断されたものは静観することの対応で問題ないものと判断します。
一方、製品品質への影響が考えられる場合には、発生した逸脱事象の根本原因の調査、発生原因と流出原因に分けて分析して解析することが必要です。
(原因解析の一例)
- 指図書の不備:条件設定の過誤、指図内容が不十分、間違った条件でも設備や作業が継続、進行させることが可能な状態となっている
- 指図書の教育が徹底されていない、指示の詳細が不明瞭等、教育・情報の不徹底の状態である
- 思い違い、勘違い、うっかりミス(ルールは知っている)
- 故意(面倒くさい、自分なりの解釈で作業が黙認される現場風土)、
時々目にする対策は、
少なくとも、是正処置は仕組みや体制の修正が必要で、教育や個人意識を高めることを対策にすることは有効とは言えないと考えます。
繰り返しお話していますが、問題発生に対する是正処置は発生防止、流出防止の両輪の対策が必要です。更に、有効性評価は、同じ製品の次回製造・生産や類似品の製造・生産で逸脱が再発していないこと、その後もある程度の期間で是正の仕組みや体制が運用状態になっていることを評価することが必要です。その確認結果で、是正処置が有効であることを評価し、適切であると判断することが必要です。
2. 逸脱のモデルケースで逸脱処理の手順と有効性評価の方法を考えてみよう!
(事例)
製造所において、A化粧水を製造中に60℃で加温した後に粉末原料Bを添加し、攪拌溶解しないといけないが、室温のまま粉末原料Bを添加し、工程を進めた。指図書では60℃にすること、液温を記録すること、溶解確認をダブルチェックすることが定められていたが、作業員Cは確認者が近くにいなかったことから自身の目視確認だけで大きな塊がないことを確認して工程を進めてしまった。最終作業まで工程を進めた時点で記録書のダブルチェックを受けた際に作業の中で液温の記載がないことから逸脱の事象であることが判明した。また、見かけ上溶液が透明であるものの、使用感でしっとりさがなく原料の完全溶解に関しても疑問が持たれた。
2.1. 製品への影響調査
粉末成分Bの溶解が不十分と考えられること、使用感に関する製品品質面でも逸脱しており、品質管理責任者の不適合品として判断、責任技術者の承認を経た後、当ロットは廃棄処分することとなった
この対応についてISOGMPの審査では問題ないと判断されていますとの説明を受けました。皆さんはどのように考えますか?
そもそも60℃の必要性の意義を作業員の方が理解していることが必要ですし、最終的に完全溶解することが必須ならば、例えば、完全溶解の確認方法として。透過率を測定する、コーンプレート粘度測定と屈折率測定と集中光源を用いた溶液の外観検査を行う等、物理測定と官能評価を組み合わせて完全溶解の確認結果が出ないと次のステップに進めない管理の仕組みまで落とし込むことが必要ではないでしょうか?
更に、有効性評価については、次回ロット生産の際にこの手順が確実に実行されていることの確認により判断することが適切と判断します。勿論、その後の生産実績対してもマネジメントレビューへのインプット情報として、再発していないことの確認と改訂された手順が確実に運用され、作業においても大きな問題なく継続実行されていることの評価結果が必要と考えます。
2ページ中 1ページ目
コメント
/
/
/
この記事へのコメントはありません。
コメント