医薬品の技術移転のポイント【第1回】
2021/04/16
品質システム
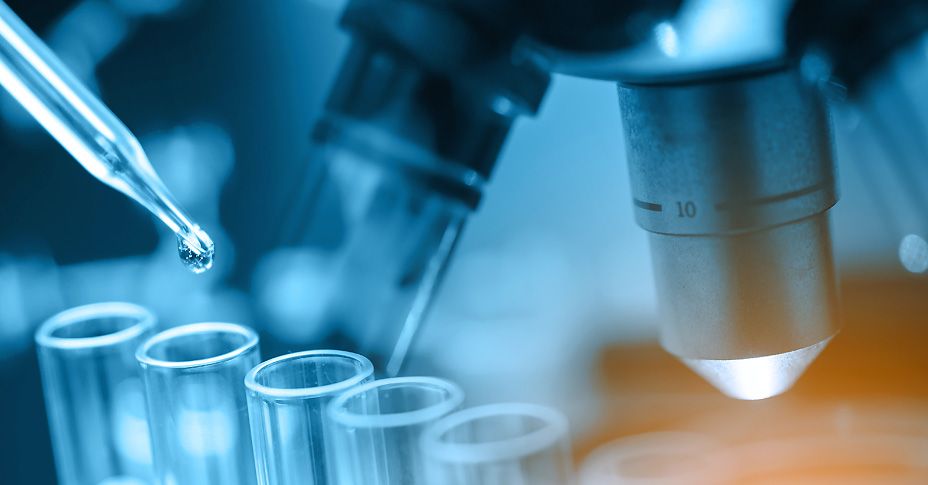
まえがき
製薬企業で30年間、品質管理/品質保証を担当し、技術移転でバリデーションを行っているのに、品質トラブルが多発することがあります。つまり、バリデーションは技術移転の一部であって、全部ではないということです。技術移転の目的は、相手先で一定の品質が確保され、計画通りに生産が行え、かつそれがコスト的にも見合った状況で医薬品製造が行われることです。
技術移転について下記の課題で注意点などを述べてみたいと思います(予定)。
1.委託先の増加
医薬品の製造所を持たなくても、医薬品の製造販売承認書を持つことができるようになり、多く企業が委託するようになりました。その理由をいくつかあげます。
1)剤型の多様化
・注射剤;シリンジ、バック
・固形剤;コールドフォーム(アルミの両面PTP)
・液剤;ゼリー など
剤形が多くなると、一品のためにその剤形の製造ラインを確保することは難しいです。また、その製造のノウハウを蓄積することも難しく、その剤形に特化した委託先、あるいは、ラインを持っていて、実績のある会社に委託します。委託する前に、新製品の開発段階から、その委託先と協力しながら申請を行います。
2)新製品の開発が続かない
・凍結乾燥製剤のラインがあっても続く製品がない
ペニシリン/セファロスポリン系の製造は、空調などを別にするために建屋を別にしています。高薬理活性は兼用ラインだと、高レベルの洗浄バリデーションが求められます。そこで設備あるいは建屋自体を別にして製造をしているのが一般になってきています。しかし、それに該当する新製品が続かないために、設備投資するだけの費用が算出できません。注射剤の製造ラインは無菌性の確保のために、常にクラスA,Bの管理をするために空調を維持管理する必要があります。製造がなくても環境モニタリングも必要です。
・コスト削減
・受託会社の方がライン稼働率が高い
・受託会社の方が新しいライン
・受託会社の方が製造コストが低い
・外部試験機関活用
設備には減価償却が発生します。それだけの費用を生産量が少ないあるいはそれほど高薬価でない製品に負わすことは赤字になります。委託先を多く訪問しましたが、委託先の方が最新鋭の製造設備を装備されていました。設備が新しく品質保証のレベルも一般に高くなっています。
人件費の問題もあります。派遣労働者が製造現場に入るようになり、従来正規社員で構成していた人員が、正規/契約/アルバイト/パート/派遣と多様化してきました。一番の目的は人件費削減です。製造コストが低い製造所は非正規労働者が多い場合があります。
導入した時点の責任者はコストを下げたと高く評価されます。ところが物事には良い面だけでなくマイナス面もあります。一般的に正規以外の方の勤続年数が短く、短期間で人が変わることです。知識や技術はどうしても人と共に存在しています。そのため、正規社員は新人の教育訓練に時間を取られていますが、そのリソースは当てが割れていません。またせっかく覚えた人が直ぐに辞められるので、知識の集積もできません。このようなマイナスのコストが出てこずに、正規社員の大きな負荷になっています。これが長い目目で見ると、品質トラブルに元凶になっているのではないでしょうか?小林化工での間違いも、未熟な作業者だったとのことです。もちろん、それ以外に多くのGMPの脆弱性とルール違反もありましたが。よって、製造コストが低いから、トータルのコストが低いことにはつながりません。小林化工の健康被害による116日の業務停止命令はまさにコストが膨大になった結果ではないでしょうか。コスト削減が創意工夫による効率によってなされているなら問題ありませんが、非正規労働やSOP違反での効率では品質の地雷を埋めているようなものです。そこに委託することの是非については十分考慮する必要があります。
3)多くの会社が製造販売と製造を別会社化&製造所の売却
大手製薬企業の多くが、製造と製造販売を別会社化にしてコスト削減を図りました。あるいは、製造所を売却した大手製薬企業も多いです。
何が発生したか?製販のQAが品質を知らなくなってきています。製造技術や品質保証は物造りと一緒に存在します。物造り失くして、品質保証はありません。
小林化工の問題で、監麻課の田中徹課長が、他社が製造販売している会社どの責任を問うています。製販であれば、対お客様/対当局の責任は製販にあるのです。製販が別で販売だけであっても、お客様は販売会社を信頼して購入しています。また、お金は販売会社に支払っています。どこで造ったかは気にせずに販売会社を信頼して購入されています。その信頼に応える品質保証ができていますか?が問われています。他社製造の委託先の場合は、それ相当のエネルギーとリソースが品質保証には必要になりますが、その理解が低いです。
製薬企業で30年間、品質管理/品質保証を担当し、技術移転でバリデーションを行っているのに、品質トラブルが多発することがあります。つまり、バリデーションは技術移転の一部であって、全部ではないということです。技術移転の目的は、相手先で一定の品質が確保され、計画通りに生産が行え、かつそれがコスト的にも見合った状況で医薬品製造が行われることです。
技術移転について下記の課題で注意点などを述べてみたいと思います(予定)。
1.技術移転の抱える問題点
2.技術移転のタイプ
3.ICH Q8 製剤開発のガイドライン
4.GMP適合性調査
5.サイト変更の技術移転時のGMP/レギュレーション(軽微・一変)
対応のポイント
6.技術移転時の品質トラブル事例
7.事前に対応を行った事例
8.レギュレーション上の課題
9.スムーズな技術移転のための方法例
10.技術移転時注意点
11.技術移管後の品質保証
2.技術移転のタイプ
3.ICH Q8 製剤開発のガイドライン
4.GMP適合性調査
5.サイト変更の技術移転時のGMP/レギュレーション(軽微・一変)
対応のポイント
6.技術移転時の品質トラブル事例
7.事前に対応を行った事例
8.レギュレーション上の課題
9.スムーズな技術移転のための方法例
10.技術移転時注意点
11.技術移管後の品質保証
1.委託先の増加
医薬品の製造所を持たなくても、医薬品の製造販売承認書を持つことができるようになり、多く企業が委託するようになりました。その理由をいくつかあげます。
1)剤型の多様化
・注射剤;シリンジ、バック
・固形剤;コールドフォーム(アルミの両面PTP)
・液剤;ゼリー など
剤形が多くなると、一品のためにその剤形の製造ラインを確保することは難しいです。また、その製造のノウハウを蓄積することも難しく、その剤形に特化した委託先、あるいは、ラインを持っていて、実績のある会社に委託します。委託する前に、新製品の開発段階から、その委託先と協力しながら申請を行います。
2)新製品の開発が続かない
・凍結乾燥製剤のラインがあっても続く製品がない
ペニシリン/セファロスポリン系の製造は、空調などを別にするために建屋を別にしています。高薬理活性は兼用ラインだと、高レベルの洗浄バリデーションが求められます。そこで設備あるいは建屋自体を別にして製造をしているのが一般になってきています。しかし、それに該当する新製品が続かないために、設備投資するだけの費用が算出できません。注射剤の製造ラインは無菌性の確保のために、常にクラスA,Bの管理をするために空調を維持管理する必要があります。製造がなくても環境モニタリングも必要です。
・コスト削減
・受託会社の方がライン稼働率が高い
・受託会社の方が新しいライン
・受託会社の方が製造コストが低い
・外部試験機関活用
設備には減価償却が発生します。それだけの費用を生産量が少ないあるいはそれほど高薬価でない製品に負わすことは赤字になります。委託先を多く訪問しましたが、委託先の方が最新鋭の製造設備を装備されていました。設備が新しく品質保証のレベルも一般に高くなっています。
人件費の問題もあります。派遣労働者が製造現場に入るようになり、従来正規社員で構成していた人員が、正規/契約/アルバイト/パート/派遣と多様化してきました。一番の目的は人件費削減です。製造コストが低い製造所は非正規労働者が多い場合があります。
導入した時点の責任者はコストを下げたと高く評価されます。ところが物事には良い面だけでなくマイナス面もあります。一般的に正規以外の方の勤続年数が短く、短期間で人が変わることです。知識や技術はどうしても人と共に存在しています。そのため、正規社員は新人の教育訓練に時間を取られていますが、そのリソースは当てが割れていません。またせっかく覚えた人が直ぐに辞められるので、知識の集積もできません。このようなマイナスのコストが出てこずに、正規社員の大きな負荷になっています。これが長い目目で見ると、品質トラブルに元凶になっているのではないでしょうか?小林化工での間違いも、未熟な作業者だったとのことです。もちろん、それ以外に多くのGMPの脆弱性とルール違反もありましたが。よって、製造コストが低いから、トータルのコストが低いことにはつながりません。小林化工の健康被害による116日の業務停止命令はまさにコストが膨大になった結果ではないでしょうか。コスト削減が創意工夫による効率によってなされているなら問題ありませんが、非正規労働やSOP違反での効率では品質の地雷を埋めているようなものです。そこに委託することの是非については十分考慮する必要があります。
3)多くの会社が製造販売と製造を別会社化&製造所の売却
大手製薬企業の多くが、製造と製造販売を別会社化にしてコスト削減を図りました。あるいは、製造所を売却した大手製薬企業も多いです。
何が発生したか?製販のQAが品質を知らなくなってきています。製造技術や品質保証は物造りと一緒に存在します。物造り失くして、品質保証はありません。
小林化工の問題で、監麻課の田中徹課長が、他社が製造販売している会社どの責任を問うています。製販であれば、対お客様/対当局の責任は製販にあるのです。製販が別で販売だけであっても、お客様は販売会社を信頼して購入しています。また、お金は販売会社に支払っています。どこで造ったかは気にせずに販売会社を信頼して購入されています。その信頼に応える品質保証ができていますか?が問われています。他社製造の委託先の場合は、それ相当のエネルギーとリソースが品質保証には必要になりますが、その理解が低いです。
3ページ中 1ページ目
コメント
/
/
/
この記事へのコメントはありません。
コメント