Investigating Out-of- Specification (OOS) Test Results for Pharmaceutical Production Guidance for Industry
医薬品製造における規格外(OOS)試験結果の調査に関する業界向けガイダンス【第4回】
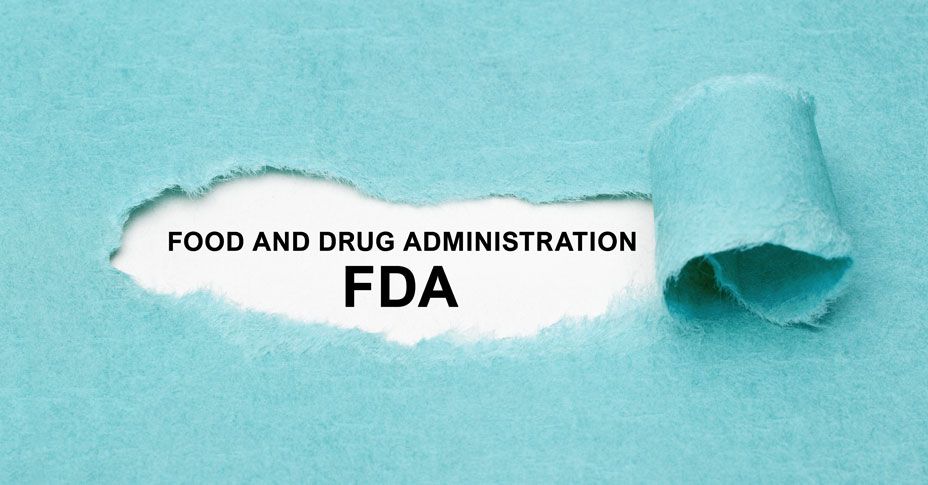
【第4回】医薬品製造における規格外(OOS)試験結果の調査に関する業界向けガイダンスの和訳。
OOS 試験結果の調査—フェーズII:本格的な(フルスケール)OOS調査
When the initial assessment does not determine that laboratory error caused the OOS result and testing results appear to be accurate, a full-scale OOS investigation using a predefined procedure should be conducted. The objective of such an investigation should be to identify the root cause of the OOS result and take appropriate corrective action and preventive action.7 A full-scale investigation should include a review of production and sampling procedures and will often include additional laboratory testing. Such investigations should be given the highest priority.
Among the elements of this phase is evaluation of the impact of OOS result(s) on already distributed batches.
初期評価でラボエラーがOOSの結果を引き起こしたと判断されず、試験結果が正確であるように見える場合は、事前に定義された手順を使用して本格的な(フルスケール)OOS調査を行う。そのような調査の目的は、根本原因を特定し、適切な是正措置や予防措置をとることにある7。フルスケール調査には製造手順とサンプリング手順のレビューが含まれ、追加の試験室試験が行われることもしばしばある。そのような調査は最優先で行うべきである。この段階の調査項目には、OOSの結果がすでに出荷されたバッチに与えた影響の評価も含まれる。
A. Review of Production 製造のレビュー
The investigation should be conducted by the QU and should involve all other departments that could be implicated, including manufacturing, process development, maintenance, and engineering. In cases where manufacturing occurs off-site (i.e., performed by a contract manufacturer or at multiple manufacturing sites), all sites potentially involved should be included in the investigation. Other potential problems should be identified and investigated.
調査はQU(QA+QC)が行い、製造、工程開発、保守管理、技術部門など、関係する他のすべての部門が関与すべきである。製造が外部で行われる場合(すなわち、委託製造先によって行われる場合や、複数の製造拠点がある場合)は、潜在的に関与する可能性のあるすべての拠点を対象とする必要がある。その他の潜在的な問題についても特定し、調査する必要がある。
The records and documentation of the manufacturing process should be fully reviewed to determine the possible cause of the OOS result(s).
OOSの原因を突き止めるには、製造工程の記録と文書を十分にレビューする必要がある。
A full-scale OOS investigation should consist of a timely, thorough, and well-documented review. A written record of the review should include the following information.
フルスケールOOS調査では、適時に徹底的なレビューを行い、そのレビューをきちんと文書化する必要がある。レビューの記録書には、以下の内容を記載する。
- A clear statement of the reason for the investigation.
- A summary of the aspects of the manufacturing process that may have caused the problem.
- The results of a documentation review, with the assignment of actual or probable cause.
- The results of a review made to determine if the problem has occurred previously.
- A description of corrective actions taken.
- 調査の理由(明確に記載すること)
- 問題の原因となった可能性のある製造工程の側面の概要
- 文書レビューの結果(実際の原因、または可能性のある原因の特定を含む)
- その問題が以前に発生したことがあるかどうかを検討した結果
- 行われた是正処置の説明
If this part of the OOS investigation confirms the OOS result and is successful in identifying its root cause, the OOS investigation may be terminated and the product rejected. However, a failure investigation that extends to other batches or products that may have been associated with the specific failure must be completed (§ 211.192). If any material was reprocessed after additional testing, the investigation should include comments and the signatures of appropriate personnel, including production and QU personnel.
この段階のOOS調査の実施により、OOSが確認され、その根本原因の特定に成功すれば、OOS調査を打ち切り、その製品を不合格にすることができる。しかし、その不具合に関連する可能性のある他のバッチや製品を対象とした不具合調査を 完了しなければならない(§211.192)。追加試験後に再加工されたものがある場合、調査の対象には、コメントと、製造およびQU担当者を含む適切な担当者の署名も含まねばならない。
OOS results may indicate a flaw in product or process design. For example, a lack of robustness in product formulation, inadequate raw material characterization or control, substantial variation introduced by one or more unit operations of the manufacturing process, or a combination of these factors can be the cause of inconsistent product quality. In such cases, it is essential that redesign of the product or process be undertaken to ensure reproducible product quality.8
OOS結果は、製品または工程設計の欠陥を示す場合がある。例えば、製品処方の堅牢性の欠如、原材料の特性評価や管理の不備、製造工程の1つ以上の単位作業によって生じるばらつき、あるいはそれらの要因の組み合わせが、製品品質のばらつきの原因となることがある。このような場合には、再現性のある製品品質を確保するため、製品や工程の再設計を行うことが不可欠である8。
7 Please note that § 211.192 requires a thorough investigation of any discrepancy, including documentation of conclusions and follow-up. Implicit in this requirement for investigation is the need to implement corrective actions and preventive actions. Corrective action and preventive action are consistent with the principles in ICH guidance for industry Q10 Pharmaceutical Quality System (April 2009). § 211.192では、結論やフォローアップの文書を含み、齟齬があった場合には、必ず徹底的な調査を行うことが求められていることに留意されたい。これは、是正措置や予防措置を行う必要性を示唆している。是正措置および予防措置はICHの業界向けガイダンスQ10 医薬品品質システム(2009 年4月)の考え方に即している。
8 OOS results might also be the result of the objectionable practice of making unauthorized or unvalidated changes to the manufacturing process. 承認を経ずに、あるいは妥当性確認を行わずに製造工程を変更するという好ましくない慣行の結果として、OOSが生じることもある。
2ページ中 1ページ目
コメント
/
/
/
この記事へのコメントはありません。
コメント