現場管理者・監督者へのメッセージ(GMPの3原則から)【第10回】
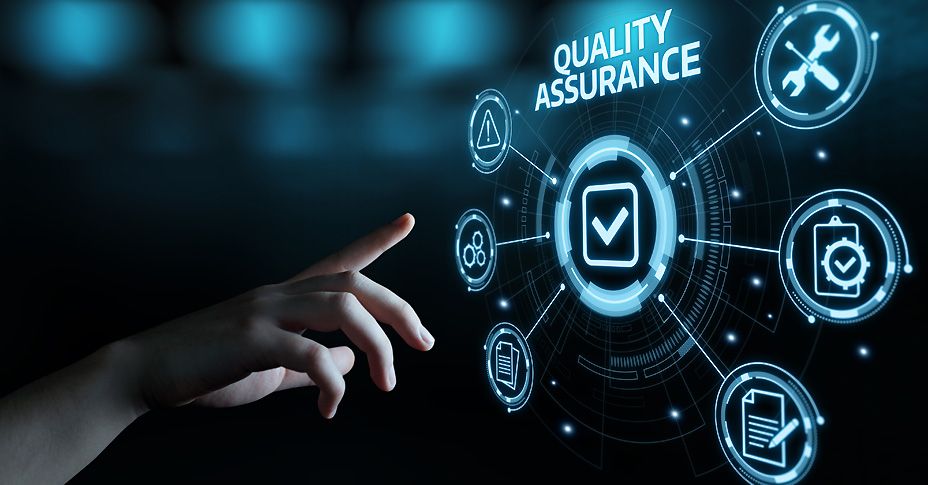
6.6.各論(6)原料から汚染:原料中の異物、原料梱包材の異物
原料入荷から使用までの一般的な例を以下に示す。
・原料入荷時にトラックヤード等で外装汚れを確認(清拭)し、指定エリアに保管「入荷」する。
・受入試験適後、工場専用パレットに載せ換え、倉庫指定エリアに搬入保管「入庫」する。
・生産計画に基づき適時、外装を再確認後、製造エリアの原料保管室(A)へ搬入する。
・原料保管室(A)から原料秤量室へ必要な原料を搬入し秤量作業に供する。
・原料元容器が段ボール(2重ポリ袋)のような軽量物の場合、原料が入った内側ポリ袋のみを取り出し、生産エリアの原料保管用容器に入れ秤量室に搬入する。余剰の原料は秤量室に隣接した一時保管室(B)に保管する。
・ドラム缶(2重ポリ袋)のような重量物の場合、ドラム缶の外装の汚れ/錆びなどを確認・清拭し、生産エリアの専用台車に載せ秤量室に搬入する。開封時はドラム缶を覆うように外装ポリ袋を折り返す。余剰の原料は元通りドラム缶に収納して、一次保管場所(A)に保管する。
これらの搬入手順をきっちり定め、作業員に徹底する。
原料秤量作業中は、原料の外観(変色、ケーキング、吸湿有無など)を確認し、かつ異物の有無を(見える範囲に限界はあるが)常に意識して作業し、もし異常があれば直ちに上司へ報告する。
特に、大量に使用する賦形剤(乳糖など)などで異物混入リスクを否定できない場合には、秤量前処理として少なくとも篩過選別を行うべきである。出来れば光学的な検査機により異物選別を行うことが望まれる。また、これらの賦形剤を含む素錠などの製剤バルクも目視検査や光学的な検査機により選別を行う必要があるだろう。
6.7.各論(7)材料から汚染:バイアル、アンプル、瓶(ガラス異物)、ポリ袋、PTPフィルムなど
基本は、やはり材料メーカーの監査・指導が重要である。
特に注意が必要なのは、バイアルやアンプルのガラス異物の混入である。バイアルやアンプルの付着異物は溶着したもので無ければ、洗浄工程のバリデーションで設定された洗浄条件で異物の洗浄除去は保証できる。ただアンプルやバイアル内に偶発的に混入したガラス片で大きい物は、洗浄工程でも洗浄針自身が出口を塞ぐことになり排除できないケースがあるので、注意しなければならない。ベンダー監査で、ガラス破片が混入しない、混入しても排除するハード面やソフト面の管理の妥当性を確認し、もし問題があれば改善指導しなければならない。
同様に、自社工程の空アンプルやバイアルの洗浄滅菌後の供給搬送部で破損した場合、破片が飛散すると考えられる搬送ライン周辺のアンプルやバイアルを全て排除・清掃をしなければならない。溶液注の場合は後工程の検査工程で光学的な検査機でほぼ確実にガラス片を含む異物の混入を検知・除去できる対策を講じることができる。一方、粉末バイアルなどでは検査機や目視検査に限界があるため、バイアル破損はより深刻な問題となる。確実に排除するため、より広範囲な搬送ライン周辺のバイアルを排除しなければならないだろう。
<バイアル充填品のインライン検査員の配置>
少し話が逸れるが、20数年前に訪問した米国の大手医薬品会社の事例である。バイアル充填後にインライン検査員が配置されていた。ユニバイアルのセンターシーリング(中間ゴム栓)の脱落有無や転倒バイアルのチェックをしていた。前工程のターンテーブル上で充填バイアルが多数転倒したため、前工程の作業員(一人作業)がターンテーブルを停止させ、転倒したバイアルを立てていた。僅か2~3m上流側のターンテーブルが止まっても、ライン検査員は持ち場を離れず椅子にただ座って待っていた。「何と非効率なのだろう、欧米人らしいな」と思った。
よく似た事象が7年程前まで筆者が勤務していたアイルランドの工場でもあった。小分包装ラインに臨時的に検査員を配置したことがあった。ラインが停止した時、その検査員は持ち場を離れずただ座って待っているだけだった。今回は自社工場である。早速「現場マネジャーに何故他の仕事を手伝わせないのか」と迫った。「アイルランドもアメリカと同じか、効率が悪いな」と思った。しかし返事は「作業員の配置が検査を目的としているため、ラインが停止しても他の仕事はさせるべきでない、インライン検査業務に専念させなければならない」というものだった。本人のその時のJob Descriptionがそうなのであろう。確かに検査で見逃しがあれば検査員の責任になる。
作業員の相互協力による生産性の向上か、検査見逃しのリスク回避を重視するか、包装作業員の熟練度や臨時的な検査(非定常作業)などの事情を考慮しなければならないが、意見が分かれるところである。
コメント
/
/
/
コメント