Some Considerations about Process Validation
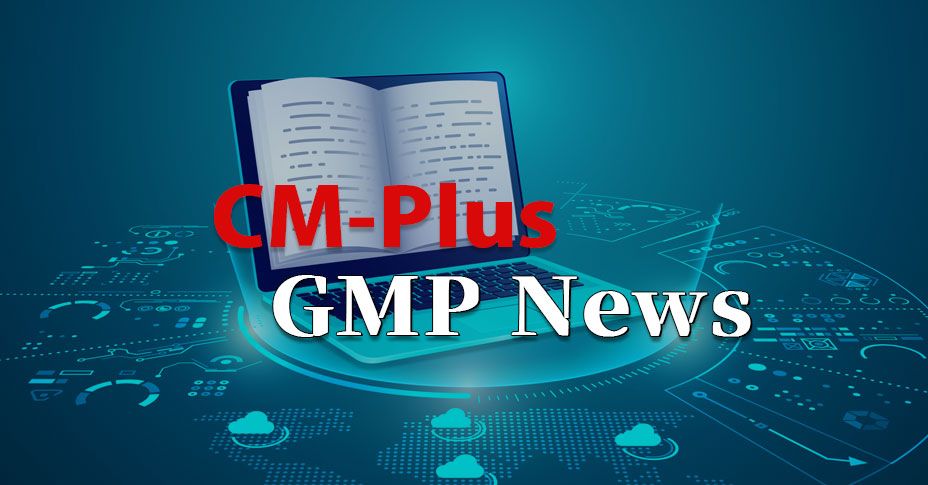
Some Considerations about Process Validation
When the FDA first introduced the concept of process validation in 1987, it defined process validation as "Establishing documented evidence which provides a high degree of assurance that a specific process will consistently produce a product meeting its pre-determined specifications and quality attributes" and required that all drug manufacturing processes be validated. Pharmaceutical companies around the world have been wondering what kind of evidence is needed to prove that a product can be manufactured consistently, and then they have been assuming without any reason that process validation is established after three consecutive batches of successful manufacturing. Once such a concept has taken root, more and more pharmaceutical companies lose the motivation to improve the process once process validation has been established due to the complexity of change management, and this results in a deviation from the original purpose of GMP, which is to improve the quality of pharmaceutical products.
To overcome this situation, the FDA revised its guidelines for process validation in 2011. According to the new definition, process validation is "The collection and evaluation of data, from the process design stage through commercial production, which establishes scientific evidence that a process is capable of consistently delivering quality product,“ and is an activity to collect and evaluate the necessary data throughout the product life cycle.
In other words, process validation has been redefined as an activity to continuously improve the process throughout the life cycle of a pharmaceutical product, rather than a one-time activity such as the successful completion of three consecutive batches. All activities that collect and evaluate necessary data throughout the lifecycle of a pharmaceutical product, starting from process development, through conventional process validation, or PPQ (Process Performance Qualification), to continuous verification in commercial manufacturing, are considered to be process validation.
Let us consider again how to proceed with process validation. A manufacturing process consists of four elements: manufacturing method, raw materials, equipment, and operator. In other words, if specified raw materials are input to specified equipment and specified operators work according to specified manufacturing methods, the system can be regarded as a system that produces the desired product as an output.
Only after qualifying these four elements, i.e., qualifying the raw materials and process in the R&D phase, qualifying the manufacturing equipment, and training the operators to be suitable for the process, can proceed to the next step, PPQ. The entire series of activities to analyze the data obtained in actual production and to improve quality throughout the product life cycle is called process validation.
The FDA's new definition was a very significant turning point, but unfortunately, the latest PIC/S GMP has also failed to break away from the conventional easy way of thinking of process validation as a transient activity of successful completion of three consecutive batches. It should be noted that even if PPQ is completed, process validation is not completed. I feel that it is difficult to overturn a once-established concept.
Among these four elements, the qualification of the manufacturing process and raw materials can be rigorously proven through small-scale experiments, and the qualification of facilities can be scientifically proven through DQ, IQ, OQ, and PQ. However, for the remaining element, the operator, there is no appropriate means other than education, training, and experience to rigorously guarantee his/her eligibility. This situation is analogous to the fact that even a person with a driver's license and great driving skills has a non-zero risk of causing an accident. No person or operator can be guaranteed to be qualified in the strict sense of the word, in the sense that no human being can fail. Therefore, it should be considered that unless a process is developed that does not involve human intervention, there is no perfect process and process validation cannot be established.
As discussed above, human-involved manufacturing processes cannot be completely validated. All we can do is to continue the qualification of the components of the process (raw materials, manufacturing methods, equipment, and personnel) and the verification of each manufacturing batch. This overall activity would be process validation.
Comment
/
/
/
There are no comments yet.
Comment